جوش لیزری
در سال های اخیر، به لطف توسعه سریع صنعت انرژی های نو، جوش لیزری به دلیل مزایای سریع و پایدار، به سرعت در کل صنعت انرژی های جدید نفوذ کرده است.در میان آنها، تجهیزات جوش لیزری بیشترین نسبت کاربرد را در کل صنعت انرژی های جدید به خود اختصاص می دهند.
جوشکاری لیزری به دلیل سرعت زیاد، عمق زیاد و تغییر شکل کوچک به سرعت به انتخاب اول در همه اقشار تبدیل شده است.از جوش های نقطه ای گرفته تا جوش های لب به لب، جوش های ایجاد شده و آب بندی، جوش لیزری دقت و کنترل بی نظیری را ارائه می دهد.این نقش مهمی در تولید و ساخت صنعتی از جمله صنایع نظامی، مراقبت های پزشکی، هوافضا، قطعات خودرو 3C، ورق های فلزی مکانیکی، انرژی های نو و سایر صنایع ایفا می کند.
در مقایسه با سایر فناوری های جوشکاری، جوش لیزری دارای مزایا و معایب منحصر به فرد خود است.
مزیت - فایده - سود - منفعت:
1. سرعت سریع، عمق زیاد و تغییر شکل کوچک.
2. جوشکاری را می توان در دمای معمولی یا در شرایط خاص انجام داد و تجهیزات جوشکاری ساده است.به عنوان مثال، یک پرتو لیزر در یک میدان الکترومغناطیسی رانش نمی شود.لیزرها می توانند در خلاء، هوا یا محیط های گاز خاصی جوش دهند و می توانند موادی را که از طریق شیشه یا شفاف به پرتو لیزر هستند جوش دهند.
3. می تواند مواد نسوز مانند تیتانیوم و کوارتز را جوش دهد و همچنین می تواند مواد غیر مشابه را با نتایج خوبی جوش دهد.
4. پس از فوکوس لیزر، چگالی توان بالاست.نسبت تصویر می تواند به 5:1 برسد و هنگام جوشکاری دستگاه های پرقدرت می تواند تا 10:1 برسد.
5. جوشکاری میکرو را می توان انجام داد.پس از متمرکز شدن پرتو لیزر، می توان یک نقطه کوچک را به دست آورد و می توان آن را با دقت در موقعیت قرار داد.می توان آن را برای مونتاژ و جوشکاری قطعات کار میکرو و کوچک برای دستیابی به تولید انبوه خودکار اعمال کرد.
6. می تواند نواحی صعب العبور را جوش داده و جوشکاری بدون تماس از راه دور را با انعطاف پذیری زیاد انجام دهد.به خصوص در سال های اخیر، فناوری پردازش لیزر YAG از فناوری انتقال فیبر نوری استفاده کرده است که باعث شده است فناوری جوش لیزری به طور گسترده تر ترویج و اعمال شود.
7. پرتو لیزر به راحتی در زمان و مکان تقسیم می شود و چندین پرتو را می توان در چندین مکان به طور همزمان پردازش کرد و شرایط را برای جوشکاری دقیق تر فراهم می کند.
کاستی:
1. دقت مونتاژ قطعه کار باید زیاد باشد و موقعیت تیر بر روی قطعه کار قابل انحراف نیست.این به این دلیل است که اندازه نقطه لیزر پس از فوکوس کوچک است و درز جوش باریک است و اضافه کردن مواد فلزی پرکننده را دشوار میکند.اگر دقت مونتاژ قطعه کار یا دقت مکان یابی تیر مطابق با الزامات نباشد، احتمال بروز عیوب جوشکاری وجود دارد.
2. هزینه لیزر و سیستم های مربوطه بالاست و سرمایه گذاری یکباره آن زیاد است.
عیوب رایج جوشکاری لیزر در تولید باتری لیتیومی
1. تخلخل جوش
عیوب رایج در جوشکاری لیزر منافذ هستند.حوضچه مذاب جوش عمیق و باریک است.در طی فرآیند جوشکاری لیزر، نیتروژن از بیرون به حوضچه مذاب حمله می کند.در طی فرآیند سرد شدن و انجماد فلز، با کاهش دما، حلالیت نیتروژن کاهش می یابد.هنگامی که فلز حوض مذاب سرد می شود تا شروع به کریستال شدن کند، حلالیت به شدت و ناگهانی کاهش می یابد.در این زمان، مقدار زیادی گاز رسوب میکند و حبابهایی تشکیل میدهد.اگر سرعت شناور حباب ها کمتر از سرعت تبلور فلز باشد، منافذ ایجاد می شود.
در کاربردهای صنعت باتریهای لیتیومی، اغلب متوجه میشویم که منافذ به ویژه در طول جوشکاری الکترود مثبت ایجاد میشوند، اما به ندرت در طول جوشکاری الکترود منفی رخ میدهند.زیرا الکترود مثبت از آلومینیوم و الکترود منفی از مس ساخته شده است.در حین جوشکاری، آلومینیوم مایع روی سطح قبل از سرریز شدن کامل گاز داخلی متراکم شده و از سرریز شدن گاز و ایجاد سوراخ های بزرگ و کوچک جلوگیری می کند.روزنه های کوچک.
علاوه بر علل منافذی که در بالا ذکر شد، منافذ شامل هوای بیرون، رطوبت، روغن سطحی و ... نیز می شود، علاوه بر این، جهت و زاویه دمیدن نیتروژن نیز بر تشکیل منافذ تاثیر خواهد داشت.
در مورد اینکه چگونه می توان بروز منافذ جوش را کاهش داد؟
ابتدا قبل از جوشکاری، لکه ها و ناخالصی های روغن روی سطح مواد ورودی باید به موقع تمیز شوند.در تولید باتری های لیتیومی، بازرسی مواد ورودی یک فرآیند ضروری است.
دوم اینکه جریان گاز محافظ باید با توجه به عواملی مانند سرعت جوش، قدرت، موقعیت و غیره تنظیم شود و نه خیلی بزرگ باشد و نه خیلی کوچک.فشار شنل محافظ باید با توجه به عواملی مانند قدرت لیزر و موقعیت فوکوس تنظیم شود و نه خیلی زیاد و نه خیلی کم باشد.شکل نازل شنل محافظ باید با توجه به شکل، جهت و سایر عوامل جوش تنظیم شود تا روپوش محافظ بتواند به طور یکنواخت ناحیه جوش را بپوشاند.
سوم، کنترل دما، رطوبت و گرد و غبار موجود در هوا در کارگاه.دما و رطوبت محیط بر میزان رطوبت سطح زیرلایه و گاز محافظ تأثیر می گذارد که به نوبه خود بر تولید و خروج بخار آب در حوضچه مذاب تأثیر می گذارد.اگر دما و رطوبت محیط بیش از حد بالا باشد، رطوبت بیش از حد روی سطح زیرلایه و گاز محافظ ایجاد می شود و مقدار زیادی بخار آب تولید می کند و در نتیجه منافذ ایجاد می شود.اگر دما و رطوبت محیط خیلی کم باشد، رطوبت بسیار کمی روی سطح زیرلایه و در گاز محافظ وجود خواهد داشت که تولید بخار آب را کاهش می دهد و در نتیجه منافذ را کاهش می دهد.اجازه دهید پرسنل با کیفیت مقدار هدف دما، رطوبت و گرد و غبار را در ایستگاه جوش تشخیص دهند.
چهارم، روش نوسان پرتو برای کاهش یا حذف منافذ در جوشکاری با نفوذ عمیق لیزری استفاده می شود.به دلیل اضافه شدن تاب در حین جوشکاری، چرخش رفت و برگشتی تیر به درز جوش باعث ذوب مکرر بخشی از درز جوش می شود که باعث طولانی شدن زمان ماندن فلز مایع در حوضچه جوش می شود.در عین حال، انحراف پرتو نیز باعث افزایش گرمای ورودی در واحد سطح می شود.نسبت عمق به عرض جوش کاهش می یابد، که منجر به ظهور حباب ها می شود و در نتیجه منافذ را از بین می برد.از طرفی چرخش تیر باعث می شود که سوراخ کوچک به همان نسبت تاب بخورد که می تواند نیروی همزن را برای حوضچه جوش ایجاد کند و همرفت و هم زدن حوضچه جوش را افزایش دهد و در از بین بردن منافذ اثر مفیدی داشته باشد.
پنجم، فرکانس پالس، فرکانس پالس به تعداد پالس های ساطع شده توسط پرتو لیزر در واحد زمان اشاره دارد که بر ورودی گرما و تجمع گرما در حوضچه مذاب تأثیر می گذارد و سپس بر میدان دما و میدان جریان در مذاب تأثیر می گذارد. استخر.اگر فرکانس پالس بیش از حد بالا باشد، منجر به گرمای بیش از حد ورودی در حوضچه مذاب می شود، که باعث می شود دمای حوضچه مذاب بیش از حد بالا باشد، بخار فلز یا سایر عناصری که در دماهای بالا فرار هستند تولید می کند و در نتیجه منافذ ایجاد می شود.اگر فرکانس پالس خیلی کم باشد منجر به تجمع ناکافی گرما در حوضچه مذاب می شود که باعث می شود دمای حوضچه مذاب خیلی پایین باشد و انحلال و خروج گاز را کاهش دهد و در نتیجه منافذ ایجاد شود.به طور کلی، فرکانس پالس باید در محدوده معقولی بر اساس ضخامت بستر و توان لیزر انتخاب شود و از زیاد یا خیلی کم بودن خودداری شود.
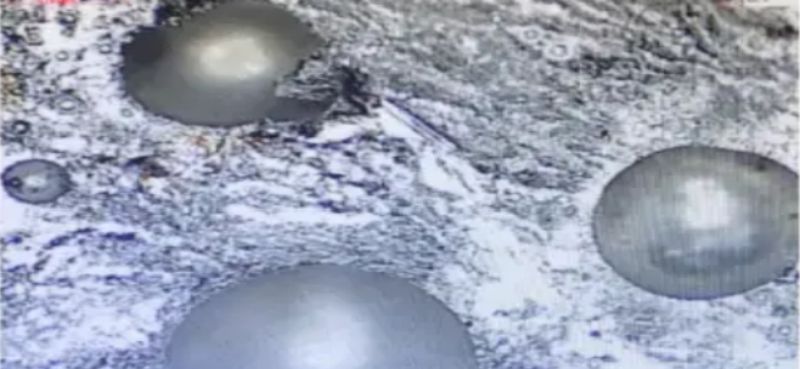
سوراخ های جوشکاری (جوشکاری لیزری)
2. پاشش جوش
پاشش ایجاد شده در طول فرآیند جوشکاری، جوش لیزری به طور جدی بر کیفیت سطح جوش تأثیر می گذارد و لنز را آلوده و آسیب می رساند.عملکرد کلی به شرح زیر است: پس از اتمام جوشکاری لیزری، ذرات فلز زیادی روی سطح ماده یا قطعه کار ظاهر می شوند و به سطح ماده یا قطعه کار می چسبند.شهودی ترین عملکرد این است که هنگام جوشکاری در حالت گالوانومتر، پس از مدتی استفاده از عدسی محافظ گالوانومتر، حفره های متراکمی روی سطح ایجاد می شود و این گودال ها در اثر پاشش جوش ایجاد می شوند.بعد از مدت ها به راحتی می توان نور را مسدود کرد و در نور جوش مشکلاتی به وجود می آید و در نتیجه یک سری مشکلات مانند شکستگی جوش و جوش مجازی ایجاد می شود.
علل پاشیدن آب چیست؟
اول اینکه چگالی توان، هر چه چگالی توان بیشتر باشد، تولید پاشش آسانتر است و پاشش مستقیماً با چگالی توان مرتبط است.این یک مشکل صد ساله است.حداقل تاکنون این صنعت نتوانسته مشکل آبپاش را حل کند و فقط می توان گفت که اندکی کاهش یافته است.در صنعت باتری های لیتیومی، پاشیدن پاشیده شدن بزرگترین عامل اتصال کوتاه باتری است، اما نتوانسته علت اصلی را حل کند.تاثیر پاشش بر روی باتری را فقط می توان از نقطه نظر حفاظت کاهش داد.به عنوان مثال، یک دایره از پورت های حذف گرد و غبار و پوشش های محافظ در اطراف قسمت جوش اضافه می شود و ردیف هایی از چاقوهای هوا به صورت دایره ای اضافه می شوند تا از ضربه پاشیدگی یا حتی آسیب به باتری جلوگیری شود.از بین بردن محیط، محصولات و اجزای اطراف ایستگاه جوشکاری می توان گفت که ابزار را تمام کرده است.
در مورد حل مشکل پاشش فقط می توان گفت که کاهش انرژی جوش به کاهش پاشش کمک می کند.در صورت ناکافی بودن نفوذ، کاهش سرعت جوش نیز می تواند کمک کننده باشد.اما در برخی از الزامات فرآیند خاص، تأثیر کمی دارد.این فرآیند یکسان است، ماشینهای مختلف و دستههای مختلف مواد اثرات جوشکاری کاملاً متفاوتی دارند.بنابراین، یک قانون نانوشته در صنعت انرژی های نو وجود دارد، یک مجموعه از پارامترهای جوشکاری برای یک قطعه تجهیزات.
ثانیاً، اگر سطح مواد پردازش شده یا قطعه کار تمیز نشود، لکه های روغن یا آلاینده ها نیز باعث پاشش جدی می شوند.در این زمان، ساده ترین کار تمیز کردن سطح مواد پردازش شده است.
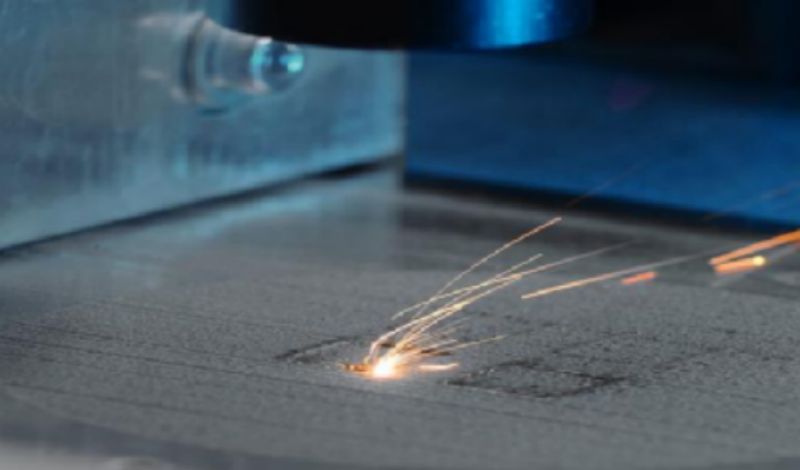
3. انعکاس بالا از جوشکاری لیزر
به طور کلی، انعکاس زیاد به این واقعیت اشاره دارد که ماده پردازشی دارای مقاومت کمی، سطح نسبتاً صاف و نرخ جذب پایین برای لیزرهای نزدیک به مادون قرمز است که منجر به انتشار مقادیر زیادی از لیزر میشود، و به دلیل اینکه بیشتر لیزرها استفاده میشوند. به صورت عمودی به دلیل مواد یا مقدار کمی شیب، نور لیزر برگشتی دوباره وارد سر خروجی می شود و حتی بخشی از نور برگشتی به فیبر انتقال دهنده انرژی جفت می شود و در طول فیبر به داخل منتقل می شود. لیزر، باعث می شود که اجزای هسته درون لیزر همچنان در دمای بالا باقی بمانند.
هنگامی که انعکاس بیش از حد در طول جوشکاری لیزری زیاد است، راه حل های زیر را می توان اتخاذ کرد:
3.1 از پوشش ضد انعکاس استفاده کنید یا سطح مواد را درمان کنید: پوشش سطح مواد جوشکاری با پوشش ضد انعکاس می تواند به طور موثر بازتاب لیزر را کاهش دهد.این پوشش معمولاً یک ماده نوری خاص با بازتاب کم است که انرژی لیزر را به جای بازتاب به عقب جذب می کند.در برخی از فرآیندها مانند جوشکاری کلکتور جریان، اتصال نرم و غیره می توان سطح را نیز برجسته کرد.
3.2 تنظیم زاویه جوش: با تنظیم زاویه جوش می توان پرتو لیزر را با زاویه مناسب تری بر روی مواد جوشکاری تابیده و وقوع انعکاس را کاهش داد.به طور معمول، برخورد پرتو لیزر به صورت عمود بر سطح ماده مورد جوش، راه خوبی برای کاهش بازتاب است.
3.3 افزودن جاذب کمکی: در طول فرآیند جوش، مقدار معینی جاذب کمکی مانند پودر یا مایع به جوش اضافه می شود.این جاذب ها انرژی لیزر را جذب کرده و بازتابش را کاهش می دهند.جاذب مناسب باید بر اساس مواد جوشکاری خاص و سناریوهای کاربردی انتخاب شود.در صنعت باتری لیتیومی، چنین چیزی بعید است.
3.4 استفاده از فیبر نوری برای انتقال لیزر: در صورت امکان می توان از فیبر نوری برای انتقال لیزر به موقعیت جوش استفاده کرد تا بازتابش کاهش یابد.فیبرهای نوری می توانند پرتو لیزر را به ناحیه جوش هدایت کنند تا از قرار گرفتن مستقیم در سطح مواد جوشکاری جلوگیری کرده و وقوع انعکاس را کاهش دهند.
3.5 تنظیم پارامترهای لیزر: با تنظیم پارامترهایی مانند توان لیزر، فاصله کانونی و قطر کانونی می توان توزیع انرژی لیزر را کنترل کرد و بازتاب ها را کاهش داد.برای برخی از مواد بازتابنده، کاهش توان لیزر ممکن است راهی موثر برای کاهش انعکاس باشد.
3.6 استفاده از تقسیم کننده پرتو: یک تقسیم کننده پرتو می تواند بخشی از انرژی لیزر را به دستگاه جذب هدایت کند و در نتیجه وقوع انعکاس را کاهش دهد.دستگاه های شکاف پرتو معمولاً از اجزاء نوری و جاذب تشکیل شده اند و با انتخاب اجزای مناسب و تنظیم چیدمان دستگاه می توان به بازتاب کمتری دست یافت.
4. زیر برش جوش
در فرآیند تولید باتری لیتیومی، کدام فرآیندها بیشتر احتمال دارد که باعث کاهش قیمت شود؟چرا کاهش قیمت رخ می دهد؟بیایید آن را تحلیل کنیم.
زیر برش، عموماً مواد اولیه جوش به خوبی با یکدیگر ترکیب نمی شوند، شکاف خیلی بزرگ است یا شیار ظاهر می شود، عمق و عرض اساساً بیشتر از 0.5 میلی متر است، طول کل بیشتر از 10٪ طول جوش است، یا طول درخواستی بیشتر از استاندارد فرآیند محصول است.
در کل فرآیند تولید باتری لیتیومی، زیر برش بیشتر اتفاق می افتد و به طور کلی در پیش جوشکاری و جوشکاری صفحه پوشش استوانه ای و پیش جوشکاری و جوشکاری صفحه پوشش پوسته آلومینیومی مربعی توزیع می شود.دلیل اصلی این است که صفحه پوشش آب بندی نیاز به همکاری با پوسته به جوش دارد، فرآیند تطبیق بین صفحه پوشش آب بندی و پوسته مستعد شکاف های جوش، شیارها، فروپاشی و غیره است، بنابراین به ویژه در معرض فرورفتگی است. .
پس چه چیزی باعث کاهش قیمت می شود؟
اگر سرعت جوش خیلی سریع باشد، فلز مایع پشت سوراخ کوچکی که به مرکز جوش اشاره دارد، زمان لازم برای توزیع مجدد نخواهد داشت و در نتیجه انجماد و زیر برش در دو طرف جوش ایجاد می شود.با توجه به شرایط فوق، باید پارامترهای جوشکاری را بهینه کنیم.به بیان ساده، آزمایشهای تکراری برای تأیید پارامترهای مختلف انجام میشود و تا زمانی که پارامترهای مناسب پیدا شوند، DOE را ادامه دهید.
2. شکاف های بیش از حد جوش، شیارها، فروریختن و غیره مواد جوشکاری، میزان فلز مذاب را که شکاف ها را پر می کند، کاهش می دهد و احتمال وقوع زیر برش ها را بیشتر می کند.این بحث تجهیزات و مواد اولیه است.آیا مواد خام جوشکاری نیازهای مواد ورودی فرآیند ما را برآورده می کند، آیا دقت تجهیزات الزامات را برآورده می کند یا خیر. رویه عادی این است که دائماً تأمین کنندگان و افراد مسئول تجهیزات را شکنجه و ضرب و شتم کنید.
3. اگر انرژی در پایان جوش لیزری خیلی سریع افت کند، سوراخ کوچک ممکن است فرو بریزد و منجر به زیر برش موضعی شود.تطابق صحیح قدرت و سرعت می تواند به طور موثری از ایجاد آندرکات جلوگیری کند.به قول قدیمیها، آزمایشها را تکرار کنید، پارامترهای مختلف را تأیید کنید و DOE را تا زمانی که پارامترهای مناسب را پیدا کنید ادامه دهید.
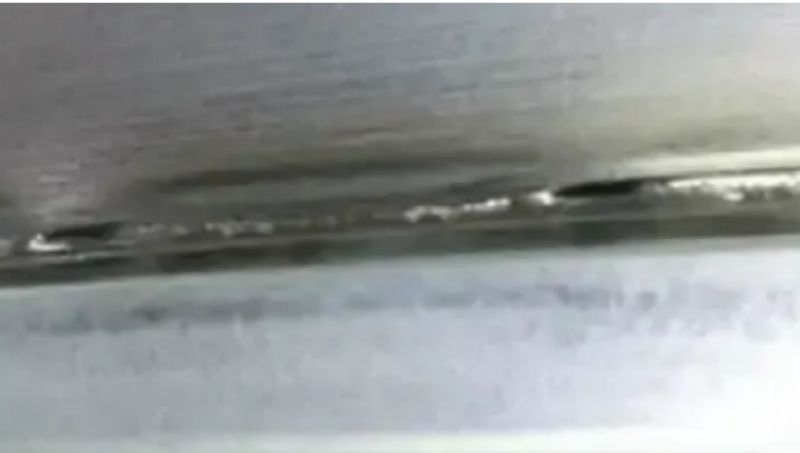
5. فروپاشی مرکز جوش
اگر سرعت جوش آهسته باشد، حوضچه مذاب بزرگتر و عریض تر می شود و مقدار فلز مذاب را افزایش می دهد.این می تواند حفظ کشش سطحی را دشوار کند.هنگامی که فلز مذاب بیش از حد سنگین می شود، مرکز جوش ممکن است غرق شود و فرورفتگی ها و گودال ها را تشکیل دهد.در این حالت، چگالی انرژی باید به طور مناسب کاهش یابد تا از ریزش حوضچه مذاب جلوگیری شود.
در موقعیت دیگر، شکاف جوش بدون ایجاد سوراخ فقط یک فروپاشی ایجاد می کند.این بدون شک یک مشکل تناسب پرس تجهیزات است.
درک صحیح عیوبی که می تواند در حین جوشکاری لیزری رخ دهد و علل عیوب مختلف، به یک رویکرد هدفمندتر برای حل مشکلات جوشکاری غیرعادی اجازه می دهد.
6. ترک های جوش
ترک هایی که در حین جوشکاری مداوم لیزری ظاهر می شوند، عمدتاً ترک های حرارتی هستند، مانند ترک های کریستالی و ترک های مایع سازی.علت اصلی این ترکها، نیروهای انقباض زیادی است که قبل از اینکه جوش کاملاً جامد شود، ایجاد میشود.
همچنین دلایل زیر برای ایجاد ترک در جوشکاری لیزری وجود دارد:
1. طراحی نامعقول جوش: طراحی نامناسب هندسه و اندازه جوش ممکن است باعث تمرکز تنش جوش و در نتیجه ایجاد ترک شود.راه حل بهینه سازی طراحی جوش برای جلوگیری از تمرکز تنش جوش است.می توانید از جوش های افست مناسب استفاده کنید، شکل جوش را تغییر دهید و غیره.
2. عدم تطابق پارامترهای جوشکاری: انتخاب نامناسب پارامترهای جوشکاری مانند سرعت جوشکاری بسیار سریع، قدرت بیش از حد بالا و غیره ممکن است منجر به تغییرات دمایی ناهموار در ناحیه جوش و در نتیجه تنش جوش و ترک های زیاد شود.راه حل این است که پارامترهای جوش را برای مطابقت با مواد خاص و شرایط جوش تنظیم کنید.
3. آماده سازی ضعیف سطح جوش: عدم نظافت و پیش عملیاتی نکردن سطح جوش قبل از جوشکاری مانند حذف اکسیدها، گریس و ... بر کیفیت و استحکام جوش تأثیر گذاشته و به راحتی منجر به ایجاد ترک می شود.راه حل این است که سطح جوش را به اندازه کافی تمیز و پیش تصفیه کنید تا اطمینان حاصل شود که ناخالصی ها و آلاینده ها در ناحیه جوش به طور موثر درمان می شوند.
4. کنترل نامناسب حرارت ورودی جوشکاری: کنترل ضعیف حرارت ورودی در حین جوشکاری مانند دمای بیش از حد در حین جوشکاری، سرعت سرد شدن نامناسب لایه جوش و ... منجر به تغییر در ساختار ناحیه جوشکاری و در نتیجه ایجاد ترک می شود. .راه حل این است که دما و سرعت خنک شدن را در حین جوشکاری کنترل کنید تا از گرم شدن بیش از حد و خنک شدن سریع جلوگیری شود.
5. تنش زدایی ناکافی: درمان تنش زدایی ناکافی پس از جوشکاری منجر به تنش زدایی ناکافی در ناحیه جوش می شود که به راحتی منجر به ترک می شود.راه حل، انجام عملیات تنش زدایی مناسب پس از جوشکاری، مانند عملیات حرارتی یا عملیات ارتعاشی (دلیل اصلی) است.
در مورد فرآیند ساخت باتری های لیتیومی، کدام فرآیندها بیشتر باعث ایجاد ترک می شوند؟
معمولاً در حین جوشکاری درزگیری ترکها مستعد ایجاد ترک هستند، مانند جوشکاری آب بندی پوسته های فولادی استوانه ای یا پوسته های آلومینیومی، جوشکاری آب بندی پوسته های آلومینیومی مربعی و غیره. علاوه بر این، در طی فرآیند بسته بندی ماژول، جوش کلکتور جریان نیز مستعد است. به ترک ها
البته برای کاهش یا از بین بردن این ترک ها می توانیم از سیم پرکننده، پیش گرم یا روش های دیگر نیز استفاده کنیم.
زمان ارسال: سپتامبر 01-2023